Precision Injection Molding Manufacturer: A Comprehensive Guide
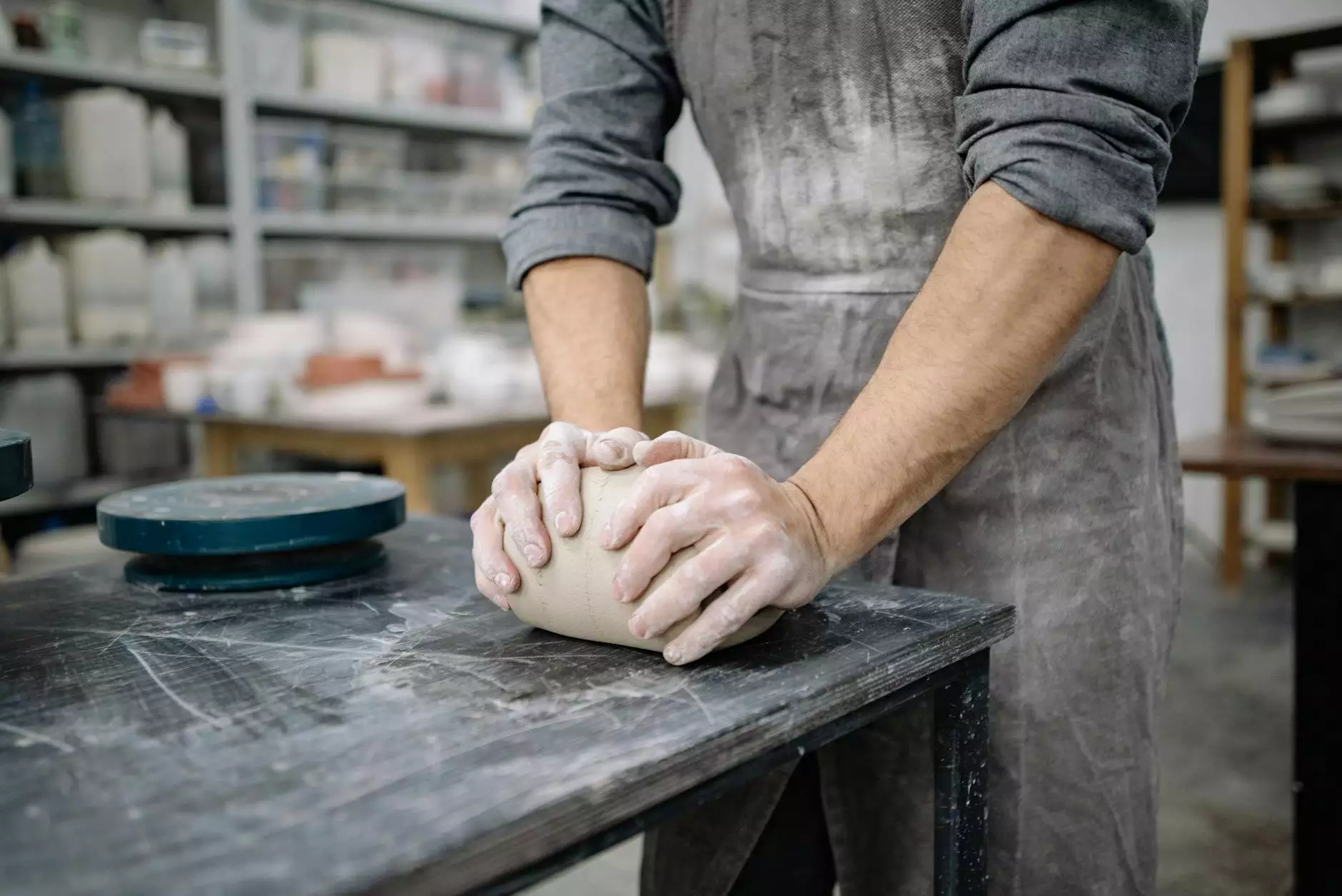
The realm of precision injection molding manufacturing plays a pivotal role in the production of an array of complex components across various industries. With the medley of technological advancements and the evolution of materials, this process has moved beyond traditional boundaries to embrace innovation and efficiency.
What is Precision Injection Molding?
Precision injection molding is a manufacturing process used to create parts by injecting molten material into a mold. This technique is renowned for its ability to produce intricate shapes with fine details and tight tolerances. It is commonly utilized in industries ranging from automotive and aerospace to consumer goods and medical devices.
The Advantages of Precision Injection Molding
- High Efficiency: The process allows for rapid production rates, making it suitable for large-volume manufacturing.
- Consistency: Precision injection molding ensures uniformity in parts, which is critical for applications requiring tight tolerances.
- Material Versatility: A wide range of materials can be used, including thermoplastics, elastomers, and even some metals.
- Cost-Effective: While the initial setup costs can be high, the per-unit cost decreases significantly at scale.
- Complex Geometries: The process can efficiently produce complex shapes that traditional methods may struggle with.
The Process of Precision Injection Molding
The injection molding process can be broken down into several critical stages that form the backbone of precision injection molding manufacturing:
1. Material Selection
Selecting the right material is crucial for achieving the desired properties in the final product. Common materials include:
- Thermoplastics: Such as ABS, polycarbonate, and nylon.
- Thermosets: Like epoxy and silicone which provide excellent heat resistance.
- Composites: For enhanced strength and lightweight applications.
2. Mold Design and Fabrication
A well-designed mold is essential for precision. Key factors include:
- The complexity of the part: More complicated parts may require more complex molds.
- Cooling channels: Efficient cooling reduces cycle time and enhances part accuracy.
- Ventilation: Proper ventilation prevents defects by allowing air to escape during the injection process.
3. Injection
The heart of the process where molten material is injected into the mold at high pressure. Precision in this step is crucial for achieving the desired characteristics.
4. Cooling
Once the material is injected, it cools and solidifies within the mold, taking on its final shape. Cooling strategies can significantly impact the speed and quality of production.
5. Ejection
After cooling, the mold opens and ejects the finished part. Care must be taken to avoid damaging the delicate features of the component.
Applications of Precision Injection Molding
The applications of precision injection molding are vast and varied. Here are some key sectors using this technology:
1. Automotive Industry
Precision parts for vehicles, such as dashboards, connectors, and housings, benefit greatly from the advantages of this manufacturing method.
2. Medical Devices
From syringes to intricate surgical instruments, precision injection molding provides the accuracy required in medical applications.
3. Consumer Products
Items like electronics casings, household items, and packaging often rely on precision molding for their production.
4. Aerospace Components
High-performance parts that must withstand extreme conditions are manufactured using advanced polymers and composites.
Challenges in Precision Injection Molding
Despite its many benefits, precision injection molding manufacturing presents challenges that must be managed effectively:
- Tooling Costs: The initial investment in high-quality molds can be significant.
- Material Limitations: Not all materials are suitable for injection molding, and choosing the right one can be critical.
- Cyclical Production: Changes in product design or demand can disrupt the optimized production schedules.
Why Choose Deep Mould as Your Precision Injection Molding Manufacturer?
When it comes to selecting a precision injection molding manufacturer, Deep Mould stands out for several reasons:
1. Expertise
With years of experience in the field, we bring unparalleled expertise that ensures quality and precision in every project.
2. Advanced Technology
We utilize cutting-edge machinery and software to optimize the design and manufacturing processes, improving efficiency and accuracy.
3. Custom Solutions
We understand that each client has unique needs, and we are committed to providing tailored solutions that meet those specific requirements.
4. Quality Assurance
Our rigorous quality control system ensures that every part produced meets the highest industry standards.
5. Comprehensive Services
From concept to production, our team supports clients through every stage of the manufacturing process, developing lasting partnerships.
Conclusion
In the evolving landscape of modern manufacturing, precision injection molding remains a cornerstone of efficiency, innovation, and quality. Choosing a trustworthy manufacturer, such as Deep Mould, is essential for achieving the best results in your production needs. With our commitment to excellence and an unwavering focus on customer satisfaction, we are eager to help you turn your ideas into high-quality, precision-engineered products.
For more information on our services and how we can assist you as a leading precision injection molding manufacturer, visit our website at deepmould.net.